La tecnica del riciclaggio a freddo nei lavori di ampliamento della strada statale 16
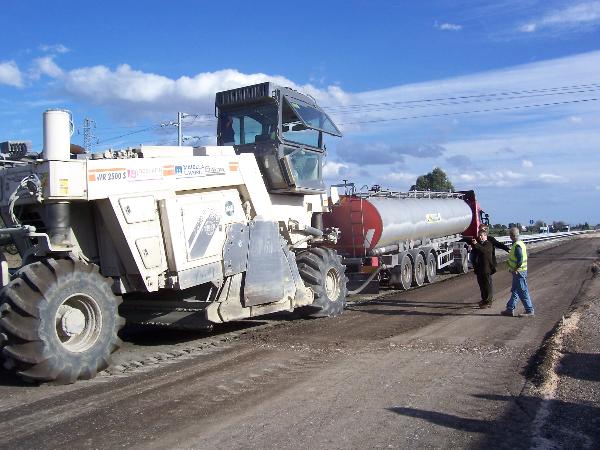
Il progetto di ammodernamento del II lotto del tronco Foggia-Cerignola sulla statale 16, prevede l’ampliamento della carreggiata da due a quattro corsie, la realizzazione dello spartitraffico centrale e di strade laterali di servizio con incroci a livelli sfalsati. Il tracciato si sviluppa in direzione ovest-est tra Foggia e Cerignola, fiancheggia sul lato destro l’abitato di Carapelle, è quasi completamente in rettifilo, a quota di poco superiore a quella del piano campagna. In corrispondenza della sede stradale esistente, per far posto alla nuova pavimentazione, è prevista la demolizione degli strati in conglomerato bituminoso con la conseguente “produzione” di circa 20 mila metri cubi di fresato.
Per evitare lo smaltimento e riutilizzare in cantiere tutta la quantità di fresato, lo strato di base è stato realizzato con una miscela riciclata a freddo con emulsione bituminosa sovrastabilizzata e cemento, in alternativa al conglomerato bituminoso a caldo previsto in progetto.
La Pavimentazione di progetto
La nuova sezione stradale è costituita da una doppia carreggiata, ciascuna di 7 m, da uno spartitraffico di 1.10 m, da due banchine laterali di 1.75 m, per una larghezza totale della piattaforma di 18.60, e da due arginelli laterali di 0.75 m. Una parte della nuova strada coincide con la sede esistente (larghezza pavimentata di m 10,50), per il resto è in allargamento su entrambi i lati di circa m 4.00 (fig. 1). Nelle zone nuove è prevista una bonifica per una profondità di circa m 1.00 dal p.c., la posa di un geotessile ed il riempimento con terre da rilevato appartenenti ai gruppi A1 e A3. Quando necessario, con le stesse terre A1 e A3 si procede alla formazione di un rilevato per raggiungere la quota di progetto del piano di appoggio della pavimentazione. In corrispondenza della strada esistente è prevista la demolizione dei vari strati fino alla quota di -54 cm per far posto alla nuova pavimentazione costituita da: fondazione in misto granulare stabilizzato di cm 35; strato di base in conglomerato bituminoso a caldo di cm 10; strato di collegamento, binder, di cm 6; strato di usura di cm 3.
La pavimentazione alternativa realizzata
La pavimentazione della strada esistente è costituta da vari strati di conglomerato bituminoso, per uno spessore complessivo di circa cm 18, e da una sottostante massicciata a penetrazione di circa 25 cm, nota anche con il nome di macadam bitumato. Quella del macadam bitumato è una tecnica in uso negli anni ’50 e ’60 che prevedeva la stesa di uno strato di pietrisco su cui si faceva “penetrare” (colare) il bitume caldo. Nonostante le quote di progetto siano sempre di 10-20 cm superiori a quelle del piano viabile attuale, l’alloggiamento della nuova pavimentazione avrebbe comportato la demolizione degli strati di conglomerato bituminoso e di tutta la massicciata in macadam bitumato con la produzione di oltre 50 mila metri cubi di rifiuti speciali. Per il macadam bitumato (circa 30 mila metri cubi), a causa delle dimensioni degli elementi più grandi (> 100 mm), non esistono reali possibilità di riutilizzo e quindi è ipotizzabile solo la destinazione a discarica. Per il conglomerato bituminoso fresato (circa 20 mila metri cubi) può essere ipotizzato un reimpiego nella confezione dei conglomerati bituminosi a caldo, ma la bassa quantità utilizzabile (15 – 20% rispetto alla massa degli aggregati) rapportata alla produzione locale di miscele a caldo fa ipotizzare tempi di assorbimento molto lunghi. Deve essere inoltre considerato che l’allontanamento dal cantiere del materiale di risulta delle demolizioni (fresato + macadam) ed il conferimento di una corrispondente quantità di materiali vergini (misto granulare per lo strato di fondazione e conglomerato bituminoso) richiedono una rilevante fase di trasporto. Ipotizzando una distanza di trasporto di circa 30 km, sia per lo stoccaggio del demolito che per il prelievo dei nuovi materiali, nell’ipotesi di progetto sarebbero necessari 5.000 viaggi di autoarticolati per complessivi 300.000 km, con un consumo di carburante di circa 150 t. E' stata pertanto valutata una soluzione alternativa che consentisse di evitare la demolizione del macadam bitumato e di riutilizzare tutto il conglomerato bituminoso fresato. Una specifica campagna di indagini (saggi, prove di carico su piastra, classificazione) ha consentito di valutare le caratteristiche meccaniche dei materiali presenti sotto gli strati di conglomerato bituminoso. In particolare le prove di carico eseguite con piastra da 300 mm di diametro hanno fornito valori del Modulo di Deformazione Md di circa 100 N/mm2 sopra alla massicciata in macadam bitumato e di 85 N/mm2 sotto la massicciata (sopra lo strato di fondazione). Sono buoni risultati, superiori a quelli prescritti dal Capitolato Speciale d’Appalto per il nuovo strato di fondazione, attribuibili alla qualità dei materiali, ma soprattutto alla compattazione prodotta nel corso di tanti anni dal consistente traffico pesante. Considerato che il misto granulare del nuovo strato di fondazione non avrebbe assicurato gli stessi valori di portanza, si è deciso di non demolire il macadam bitumato. Per verificare che gli stessi livelli di portanza, accertati in singoli punti con la prova di carico su piastra, fossero presenti su tutta la vecchia pavimentazione, è stata utilizzato un rullo equipaggiato con compattometro. Dopo la fresatura del sovrastante conglomerato bituminoso tutta la superficie è stata “tastata” dal rullo che ha registrato i corrispondenti valori del modulo elastico della massicciata in macadam bitumato. Nelle poche zone dove il modulo è risultato inferiore a 80 N/mm2 è stata realizzata una bonifica mediante sostituzione del macadam con misto granulare stabilizzato. Nelle zone in allargamento, come previsto dal progetto, è stata eseguita la bonifica del sottofondo, l’eventuale formazione del rilevato e la posa dello strato di fondazione con misto granulare stabilizzato. Perseguire l’obiettivo di riutilizzare tutto il fresato è stato più facile. Lo strato di base previsto in 10 cm di conglomerato bituminoso a caldo è stato sostituito da 15 cm di una miscela di aggregati e fresato, stabilizzata a freddo con cemento ed emulsione bituminosa sovrastabilizzata Rigeval. L’aumento di spessore dovrebbe compensare le inferiori caratteristiche meccaniche della miscela fredda rispetto al conglomerato a caldo. Per confrontare il livello prestazionale della pavimentazione alternativa rispetto a quella di progetto è stato eseguito il calcolo con metodo razionale mediante il software BISAR della Shell Research utilizzando parametri largamente diffusi e condivisi a livello scientifico. La vita utile della pavimentazione alternativa è risultata sensibilmente superiore rispetto a quella della pavimentazione, confermando che l’incremento di spessore del 50% (da cm 10 a cm 15) compensa le minori prestazioni della miscela fredda. Lo strato di base riciclato a freddo è stato previsto per tutta la larghezza della nuova pavimentazione (m 18.60), mantenendo invariato lo spessore del binder e del tappeto di usura .
Materiali impiegati
Le miscele bituminose a freddo per strati di base sono usualmente costituite da materiali di riciclo della vecchia pavimentazione, eventuali aggregati vergini di integrazione, da bitume schiumato o emulsione bituminosa e da cemento. Nel caso specifico, nell’alternativa tra il bitume schiumato e l’emulsione bituminosa, si è deciso di utilizzare l’emulsione bituminosa sovrastabilizzata, cioè a rottura molta lenta. L’impiego dell’emulsione non richiede il riscaldamento del legante oltre i 160 °C, come per il bitume schiumato, evitando rischi per gli addetti ed una maggiore flessibilità nella gestione dei tempi di attesa prima della miscelazione. Grazie ai tempi di rottura molto lunghi, consente inoltre di gestire con maggiore margine temporale le fasi di compattazione e livellamento senza pregiudicare la buona riuscita del trattamento. La miscela granulare è costituita da circa il 65% da conglomerato bituminoso fresato della pavimentazione esistente e, per il resto, da misto granulare naturale (di primo impiego). L’integrazione del fresato con misto granulare tende a garantire un buon assortimento granulometrico nel rispetto del fuso granulometrico indicato nella successiva tabella 1. Si evidenzia che per questo tipo di miscele non è molto rilevante la dimensiona massima degli aggregati ma piuttosto la quantità dei fini e la distribuzione granulometrica regolare (curva continua). Nella determinazione della curva granulometrica, in particolare nella valutazione del passante al setaccio da 0,063 mm è stato considerato anche il cemento, nella quantità effettivamente impiegata. Come legante bituminoso è stata impiegata emulsione bituminosa sovrastabilizzata Rigeval, specifica per le miscele contenenti cemento.
Studio della miscela
In alternativa allo studio di laboratorio, le percentuali ottimali di cemento, acqua ed emulsione bituminosa sono state definite con un campo prova in vera grandezza. Questo ha consentito di evitare le difficoltà di trasferimento in cantiere delle risultanze degli studi di laboratorio, difficoltà dovute alle differenti modalità di miscelazione e compattazione dei materiali. Per una corretta valutazione delle caratteristiche granulometriche della miscela il prelievo degli aggregati è stato eseguito dopo un passaggio di pulvimixer in modo da poter considerare l’effetto di sgranamento del fresato prodotto dalla macchina stabilizzatrice. Sono stati realizzati tratti con differenti quantità di emulsione bituminosa e cemento: il primo test è stato fatto con la quantità 1,5% di cemento dosando il 3% e il 3,5% di emulsione Rigeval ; il secondo test è stato fatto con la quantità 2% dosando sempre le stesse percentuali di emulsione. Subito dopo la miscelazione con il pulvimixer, per ogni tratta con differente dosaggio, sono stati prelevati campioni per la confezione di provini con pressa giratoria (UNI EN 12697-31). Su tali provini, dopo una maturazione a 40 °C per 72 ore e successivamente, dopo condizionamento per 4 ore in forno a 25 °C, sono stati determinati: la resistenza a trazione indiretta e il modulo di rigidezza (UNI EN 12697-26 Annesso C).
La sperimentazione in campo prova ha consentito di individuare come dosaggi ottimali il 2% di cemento ed il 3% di emulsione bituminosa sovrastabilizzata.
Modalità Operative (realizzazione dello strato di base a freddo)
Dopo aver verificato le quote, la sagoma e la portanza sullo strato di fondazione è stato riportato il conglomerato bituminoso fresato, spianato fino a formare uno spessore di circa cm 12 e successivamente il misto granulare per uno spessore di circa 5 cm. Lo spessore soffice, complessivo, dei due materiali deve essere tale che dopo l’aggiunta dei leganti (cemento ed emulsione bituminosa), la miscelazione e la compattazione lo spessore finale risulti di almeno cm 15. Poiché diversi fattori incidono sul “calo” della miscela, lo spessore soffice della miscela degli aggregati è stato determinato in campo prova. Sopra agli aggregati, immediatamente prima della miscelazione, è stato steso il cemento mediante apposito automezzo attrezzato con dosatori volumetrici. Il trattamento di miscelazione è stato realizzato con un “treno” di riciclaggio costituito da: autobotte per l’acqua, autobotte per il legante bituminoso, macchina stabilizzatrice (pulvimixer), livellatrice, rullo monotamburo vibrante e rullo gommato. Subito dopo la miscelazione, prima di eseguire il livellamento dell’impasto con il grader, è stato necessario procedere ad un primo costipamento mediante di un rullo liscio, monotamburo, vibrante per omogeneizzare l’addensamento della miscela soffice rispetto a quello prodotto dalle ruote della macchina stabilizzatrice. Successivamente, la compattazione è stata portata a termine mediante l’impiego di un rullo vibrante di 18 ton con controllo di frequenza e di ampiezza di vibrazione e di un rullo gommato di carico statico > 25 ton. Per proteggere lo strato finito dagli agenti atmosferici e garantire una regolare maturazione, al termine della rullatura è stato steso un velo protettivo di emulsione acida al 55% di bitume in ragione di 1,2 kg/m². Per evitare che tale protezione possa essere danneggiata dai mezzi di cantiere in transito, l’emulsione è stata ricoperta con graniglia.
Conclusioni
L’applicazione realizzata nell’ambito dei lavori di allargamento della statale 16 "Adriatica", 2° lotto del tronco Foggia-Cerignola, ha consentito di verificare e confermare i punti di forza del riciclaggio a freddo. La sostituzione dello strato di base a caldo con una miscela a freddo ha evitato il conferimento in discarica del fresato della vecchia pavimentazione (circa 20.000 metri cubi) ed il prelievo di aggregati da cave di prestito per la confezione del nuovo conglomerato bituminoso, riducendo notevolmente anche le fasi di trasporto da e per il cantiere: circa 5.000 viaggi di autoarticolati per complessivi 300.000 km, con un consumo di carburante di circa 150 t. A questo deve essere aggiunto il risparmio di combustibile che si sarebbe dovuto “bruciare” per riscaldare il bitume e gli aggregati lapidei nella produzione della miscela a caldo. L’impiego del treno di riciclaggio, che permette di realizzare notevoli quantità giornaliere, e la forte diminuzione dei trasporti, consentono di ridurre in modo significativo i tempi delle lavorazioni. Migliorano inoltre le condizioni di lavoro degli operai non esposti ai fumi e alle alte temperature tipiche dei conglomerati a caldo. Dal punto di vista prestazionale il confronto tra la base a caldo e quella a freddo eseguito mediante il calcolo razionale delle due pavimentazioni ha evidenziato che l’incremento di spessore del 50% (da cm 10 a cm 15) compensa ampiamente le minori prestazioni della miscela fredda.